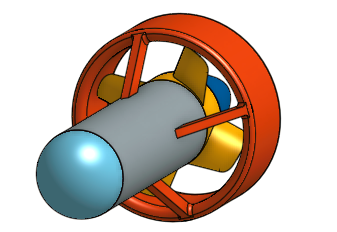
Aquanauts’ prototype magnetically coupled brushless DC thruster.
A significant challenge in underwater robotics systems is ensuring the reliability of all seals and pressure housings. In the context of vehicle propulsion this challenge is exacerbated by any attempt to adapt conventional ship propulsion to subsea use.
On any vessel featuring an inboard or outboard motor, one will find mechanical shaft seals or gland stuffing boxes on the propeller shaft. These are both employed to prevent the ingress of water (often into oil lubricated housings around the shaft or gears) and at the same time minimize the resistance on the drive shaft. Such systems have two major problems: first they have limited lifespans due to wear from the shaft and second, they can with stand a minimal pressure gradient meaning at depths below a few meters the internal housing requires pressure compensation to minimize this pressure gradient and prevent leaks.
While shaft seals are adequate for surface vessels, the depths at which ROVs operate necessitates extensive pressure compensation for any chance of success. One of the few alternatives which exist involves encasing a brushless motor’s stator in epoxy to insulate it from water. This, however, does not entirely solve the impacts of corrosion as the motor shaft remains exposed to water and must be regularly serviced to ensure seizing does not occur.
Our intended solution is to build a set of small magnetically coupled brushless thrusters. These work on the same principle as a brushless motor, but require the development of a custom stator to live in a sealed housing. Furthermore, an integrated rotor/propeller must also be developed to slide onto the aforementioned housing. The major obstacle here is to develop a rotor with geometry that minimizes the air gap between it and the stator. The images show document our prototype to date. The current thruster includes a kort nozzle to improve the thrust at the low speed it is intended to operate at. The yellow propeller is likely to change once we establish the maximum torque the motor is able to handle and how many and what pitch is appropriate for the blades.
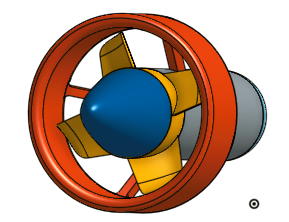
Rear view of the magnetically coupled thruster.