In the automotive industry, the integration of composite materials into the fabrication of certain car components has become increasingly popular. Particularly in the case of forming lighter components. Car manufacturers have been developing novel and innovative materials in the pursuit of weight reduction, where they have achieved it using short-fibre reinforced polymer (SFRP) composites.
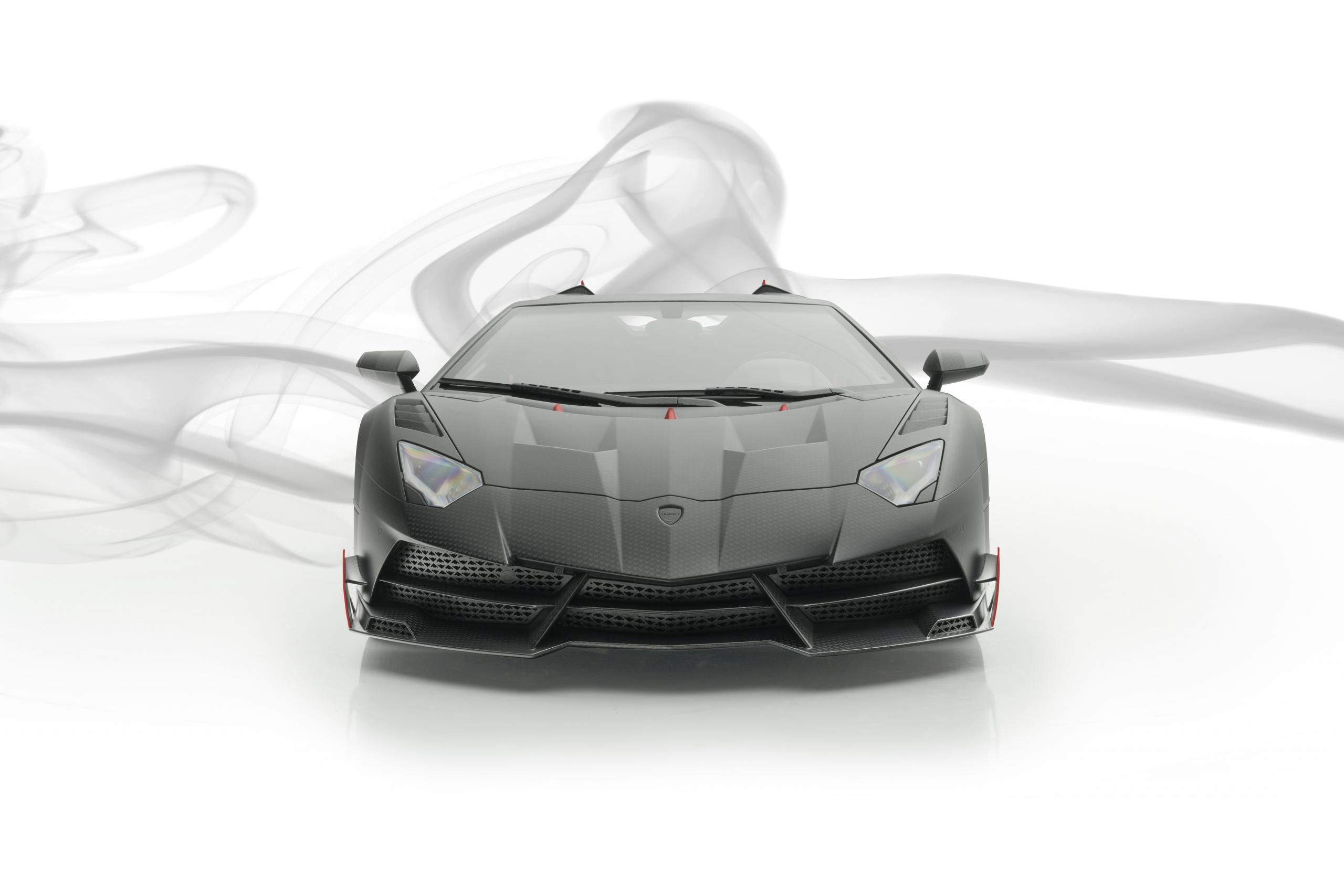
Mansory Carbon Fiber Bonnet Source: Mansory Copyright: 2020 Mansory Design & Holding GmbH
As the name suggests, SFRPs are composite materials with short length fibers that are discontinuous. This composite is easy to synthesize and has excellent mechanical properties, making it quite an interesting, yet practical, material. Furthermore, incorporating carbon short fibers is advantageous, as it is light, corrosion-resistant and quite cheap.
With the backing from the Standard and Industrial Research Institute of Malaysia (SIRIM) and Ministry of Science, Technology, and Innovation (MOSTI) in Malaysia, Rezaei et al. were able to formulate and characterize short-carbon-fiber-reinforced polypropylene (SCF/PP) composites, with the intention of replacing the more traditional steel bonnet.
To synthesize the SCF/PP, the researchers used Titanpro SM950 Polypropylene Copolymer as their matrix and Composite OracleTM, Torayca T700S 12 K acted as their reinforcing carbon fiber. They were then able to prepare 5 composite samples of varying carbon fiber sizes by blending the short carbon fiber and polypropylene. Pellets of the material were then formed and subsequently pressed. This technique is a common method used to generate carbon-fiber-reinforced-thermoplastics. Density tests and Thermogravimetric analysis (TGA) were two techniques used to characterise the material. These properties are important factors that need to be considered when making a bonnet.
From the density test data, it is evident that the composite density increased with increasing fiber content used. This was expected since the density of CF (1.80 g/cm3) is greater than the PP (0.89 g/cm3). However, the composite density decreased with the increase in the CF length. The graph below illustrates this trend for 7% CF content.
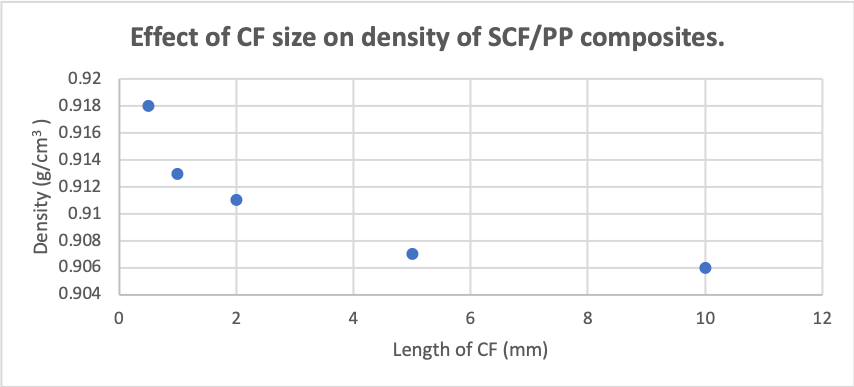
Figure 1. Effect of CF size on the density of SCF/PP composites
One proposed explanation is that there is a reduction in the voids and vacuoles, which allows the composite to pack more tightly. However, they also suspect that there is a better distribution of short fibres embedded within the PP framework, which is likely to reduce the number of voids.
The TGA data is important as it is often used in the determination of the end use. From the data, it is evident that the introduction of CF fibers to the PP matrix, improved composites ability to withstand degradation. Furthermore, heat was used to begin the degradation processes and the overall structure was either ruptured or split. The graph below depicts the degradation of the samples with 7% fiber content.
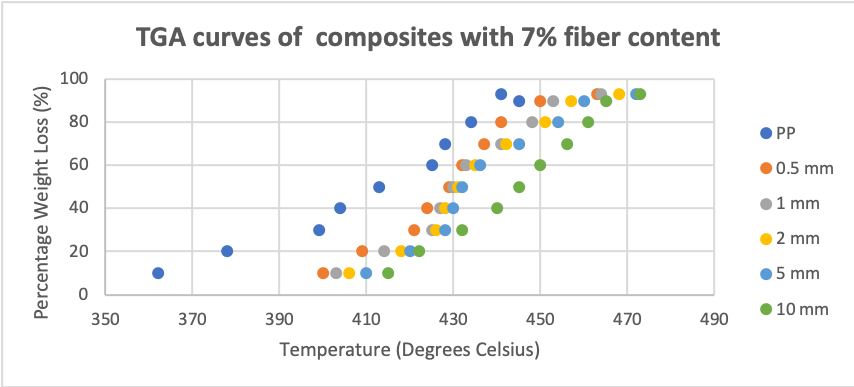
Figure 2. TGA curves of composites with 7% fiber content
As more CF is added to the PP matrix, the heat absorption capacity of CF is higher than that of PP and thus the composite will withstand degradation. Furthermore, the data suggests that as the lengths of fibers increased, the fibers in the composites absorbed more heat.
These two properties and the relative ease of forming SCF/PP composites demonstrate the efficacy and effectiveness of the material in the fabrication of a bonnet.