Week 9 (March 12-18)
Robot and mold design for a first prototype. Some thoughts on user studies.
Robot Shape
After integrating the feedback from other SPINners with the storyboarding elements, I decided that the first robot to be prototyped will be a dewdrop-shaped water-chamber purring robot. Although the egg shape was also well-received, I was a little concerned about the volume of water that the robot would have to hold – would that much water eventually interfere with purring conductance? Would it be so top-heavy that the robot would tip over?
(I was also still slightly biased because, well. Tribbles.)
In any case, I definitely plan to make more than one final robot shape after the initial prototyping proves functional, so I thought that choosing the simplest first-pass shape made the most sense.
(Also. Just. Tribbles.)
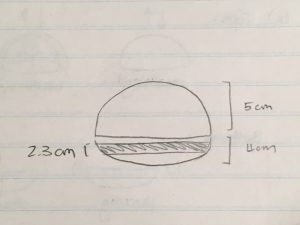
The design I settled on for a first prototype.
Mold design
Now deciding on the shape of the first full-size prototype, the next step was to design the mold – making good use of the lessons we learned from the test mold:
1) Added more air channels into the dome part of the mold (the “top” of the robot) to help with mold disassembly.
2) Designed the motor housing part of the mold (the “bottom” of the robot) to come apart in several pieces, to hopefully circumvent any possible difficulties in prying a large solid chunk of silicone out of the mold.
3) Using mold release agent to facilitate removal.
(Fingers crossed that paying attention to these particular points will be enough to make for a smoother molding experience, despite my unfortunate track record.)
An interesting issue I had to resolve with the full-size mold that did not come up during small-scale testing was the problem of how exactly do we put the water in the robot, and how do we keep it there?
After a lot of thought, we settled on:
1) Firmly gluing (via silicone; see Week 7) the robot top to the robot bottom to create the water chamber. Designed the mold to facilitate this by creating extra surface area for better adhesion – hopefully this would make the seams strong enough to hold against water pressure, and slight squeezing pressure.
2) Designing a reinforced opening in the robot top to allow water to be channeled in. Ideally, the process would not be any more complicated than filling a water bottle with a really small top.
3) 3D printing a plug to fit snugly into the opening, to prevent the water from spilling out.
Theoretically, this would be a good design, but as with everything in this lab, the only way to be sure is to actually put it to the test!
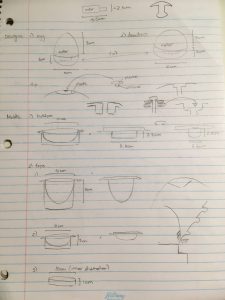
Mold design (design in general, actually) is a very messy process…
User studies
Had some conversations about user studies, and what kind of user study would best suit this robot in particular.
It turns out that there are a lot of nuances to user studies that I’ve never really noticed, having only been on the other side (i.e. the participant side) of psych studies.
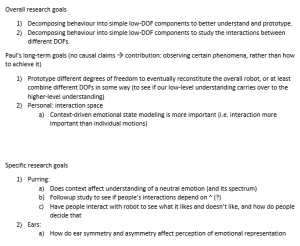
Some thoughts while considering possible user studies.
It has also become pretty apparent at this point that we won’t have time for user studies before the conclusion of the COGS 402 course, but I definitely do want to see where this project can go, so we’re aiming to do some studies over the summer, instead of rushing for the COGS deadline.