Construction, demolition, and renovation (CRD) wood waste represents a significant proportion of Canadian waste. Nationally, 10% of all residual solid waste and 40% of CRD waste is wood.[1] Our ability to successfully reuse and recycle wood materials is dependent on our ability to extract those materials from the built environment at the end of a building’s useful lifespan. Typical construction does not allow for easy material salvage as non-reversible connections and adhered layers (such as self-adhered membranes, adhesives, and sprayed insulation) prevents easy deconstruction and material salvage. This project expands on our previous work in design-for-deconstruction for light wood frame. The previous research included the development of a mock-up wall section constructed using design-for-deconstruction principles. This mock-up was subsequently deconstructed to test the ease of disassembly and the quality of materials salvaged from the deconstruction. This phase of research also produced assembly details of that mock-up and a number of other potential configurations that would allow for a variety of insulative values. The constructed mock-up was designed with an R-22 effective insulation factor to conform with the recommended requirements established by the city of Vancouver.[2]
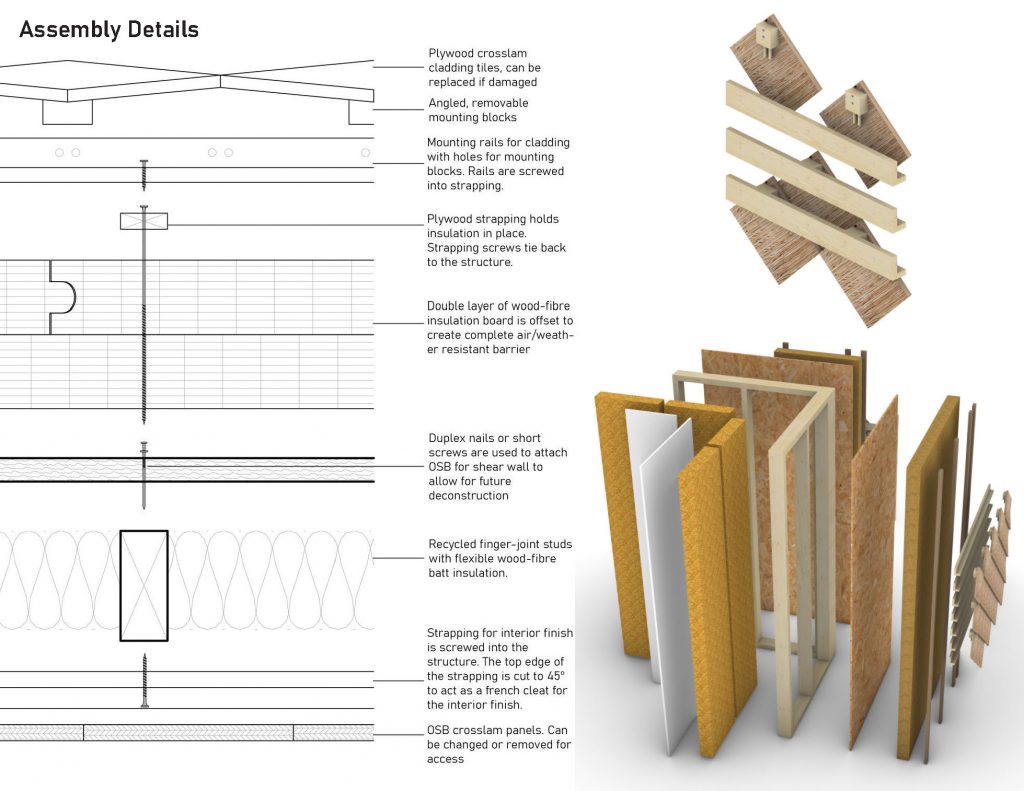
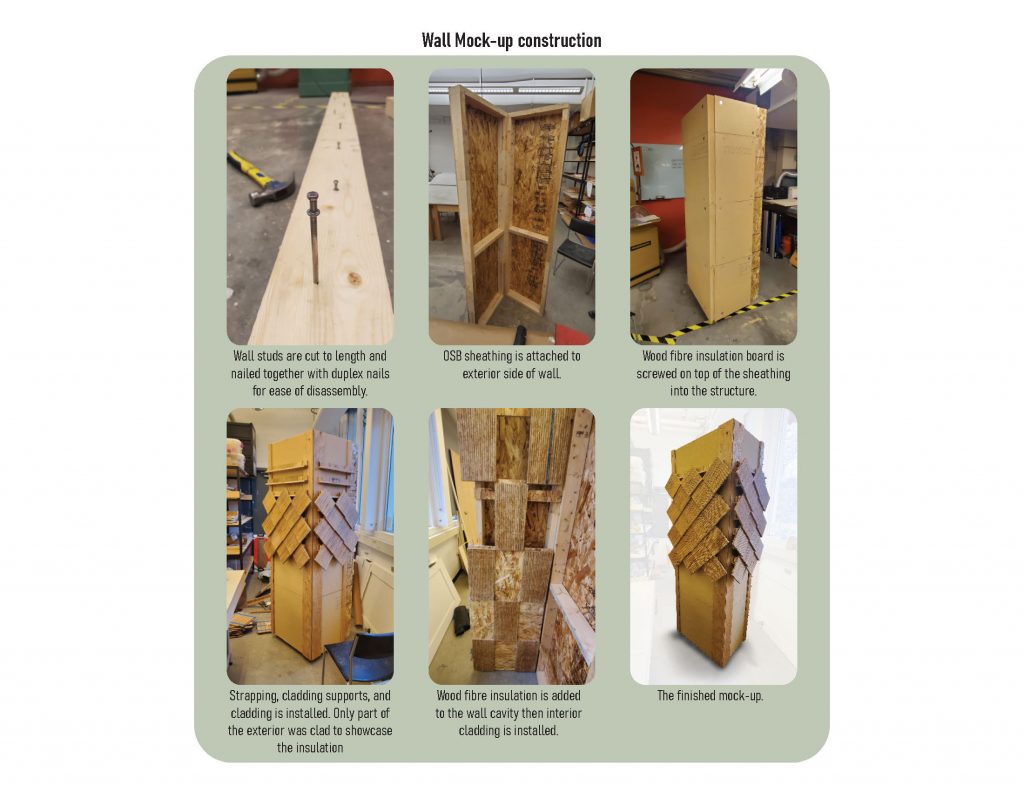
