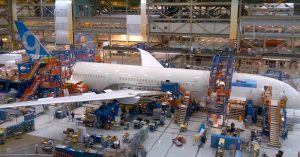
A Boeing 787 Dreamliner being assembled
The Boeing 787 Dreamliner was a beautiful idea theoretically: a revolutionary commercial plane exceeding customers’ needs with innovative design and technology. However, the combination of an ambitious vision with naive planning by management almost destroyed the 787.
The C-suite should have married cutting-edge innovation with tried and trusted manufacturing practices; instead, they took the easy route of excessive outsourcing. Unlike Apple’s in-house design of prototypes and outsourced manufacturing1, Boeing decided to transfer the responsibility of design and engineering to its suppliers. According to Eamonn Fingleton, “seventy percent (70%) of the 787 is being manufactured outside the United States, significantly more than the two percent (2%) utilised for the 747 in the late 1960s.” 2
In his blog post, Vernon Grose shares his insight that Boeing had lost its sense of wholeness of design present in its earlier planes3. I concur with his rhetoric that there is nothing wrong with outsourcing manufacturing per se, but the extent to which Boeing outsourced design and engineering of the 787 was significant and entailed considerable risk. Grose’s blog post is insightful, from his own professional experience from working at Boeing during the development of the 707; as a former employee, he has an insider’s perspective combined with an outsider’s objective criticism. Through reading his post, I was able to glean new perspectives about the case, such as the cohesive supervision of outsourcing.
If Boeing had paired its own in-house designs with outsourcing of manufacturing, the 787 would have been an innovative success. Rather, the lack of design input, guidance, communication, and collaboration with their suppliers lead to countless technical problems and delays with development and production. My recommendations to Boeing for future improvements are issue prevention, inclusive supplier-customer relationships, and overall design leadership.
Preventing problems by fostering mutual communicative relationships with suppliers would have saved Boeing time, effort, and money. A diverse and responsible management team should have included a Supply Chain Risk Management expert and more involvement in the process of development and production. Only then would outsourcing be viable.
Instead of “[reducing] the 787′s development time from six to four years and development cost from $10 to $6 billion” 4, as Boeing so proudly trumpeted, outsourcing proved to be the proverbial Achilles’ Heel. The decision to outsource engineering design for such a complex and precise machine was a problem waiting to happen, and should have been prevented from the onset. Penny-wise, pound-foolish was the name of Boeing’s game then.
Word count: 407
Photo credit:
Source: http://www.modernairliners.com/wp-content/uploads/2015/07/787-9-Final-Assembly-Web.jpg; Image © Boeing
End Notes:
1: Kabin, Benjamin. “Apple’s IPhone: Designed in California But Manufactured Fast All Around the World (Infographic).” Entrepreneur. Entrepreneur Media, Inc., 11 Sept. 2013. Web. 27 Sept. 2016.
2: Fingleton, Eamonn. “The Boeing 787: The Truth Finally Hits The Fan.” Forbes. Forbes Magazine, 26 Jan. 2013. Web. 28 Sept. 2016.
3: Grose, Vernon. “Boeing’s Global Supply Chain Created Subtle Risks for 787 Dreamliner.” Boeing’s Global Supply Chain Created Subtle Risks for 787 Dreamliner. Omega Systems Group Incorporated, 28 Jan. 2013. Web. 29 Sept. 2016.
4: Denning, Steve. “What Went Wrong at Boeing?” Forbes. Forbes Magazine, 21 Jan. 2013. Web. 26 Sept. 2016.