My lunch usually consists of two main staples every day which are Western Family sirloin steak, and Dempsters whole grain bread. Having food available through local producers such as Western Family is essential in making sure there is minimal energy outputs needed to source the products out. The company is based out of Oregon, USA which is close enough to Vancouver that systems such as transportation can minimize their energy impact.

Steak:
The steak I ate was a sirloin which is usually cut from the rear of a cow. Steak is a very good source of protein and fats which is crucial to any diet. Before I came to understand the processes of creating different foods, I didn’t realize there was so much energy needed to get a cut of steak to the consumer. However, after thoroughly investigating the steps there are in order to get the steak to retailers, I found out that there is much more to the picture.
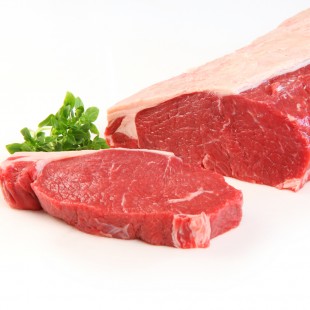
Production
For many companies that produce steak, they have systems set in place that require a lot of energy through use of machines and technology. The beef cow is raised in confined areas so they can gain weight quickly. These facilities have automated feeding stations with conveyor systems to transport the food throughout the facility. Once the cow has reached the required size they are transported by trucks to the slaughter houses. The slaughter house is a complete production facility to process the cow from the time they leave the truck until they are processed into sections or into cuts of beef for the consumer. While a large hands-on approach is required to process cattle large sections of the facility require refrigeration. This consumes large quantities of energy. The video link below demonstrates part of the meat production.
The Meatrix 2 1/2
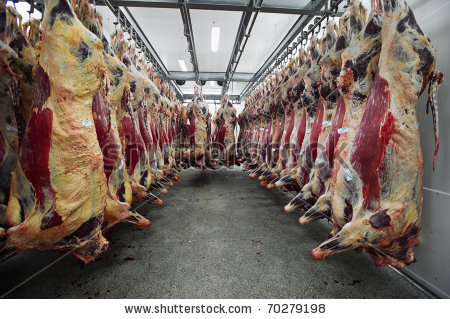
As you may be able to tell from the video, the production of meat, particularly steaks in this situation, requires an enormous amount of energy through machines. These systems of conveyer belts, cutters, and disposal bins need large volumes of energy in order to operate leading to increase emissions of fossil fuels to the atmosphere. The video gives notice that a slaughter house can process up to 5000 cows in a single day which of course means there is powerful machinery aiding in this efficient process. Cows are brought in through hanging hooks that rotate through a system of blades which cut them up into smaller pieces, they are then cleaned in order to relieve any harmful substances. The pieces of meat are then brought down through a conveyer belt which employees are able to separate the usable pieces from the not usable (human consumption). After this is done, they meat is packaged and sent off to retailers abroad. It’s a costly system that needs significant amounts of energy to operate and produce at such quick and productive paces.
Transportation
The Steak I ate was produced by the company Western Family which as I mentioned above is located in the state of Oregon, USA. There is a huge benefit in buying products from close proximities as there requires much less transportation in order to get the products to retailers and ultimately consumers. The majority of energy outputs throughout transportation is through consumption of diesel fuel. The engines on these trucks run constantly to ensure the cooling systems continue to operate and the meat does not spoil.
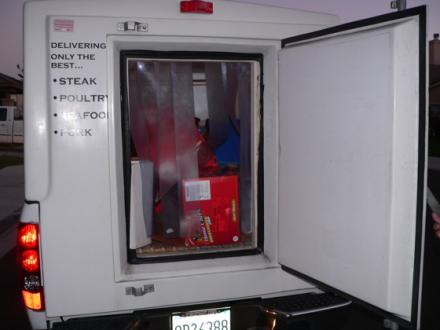
Along with the fuel required to get from one place to another and the requirement for refrigeration/freezer systems to run constantly large volumes of fuel is required to get the product to the consumer. The burning of fossil fuels is the leading source of greenhouse gas emissions and continues to grow every day.
Packaging
The meat that I purchased came in a vacuum sealed package that allocated for four strips of 8oz sirloin steaks. The package consists of a foam like material on the bottom with a clear surrand wrap over the top to keep the meat sealed and ready to be cooked. The material used in the packaging is produced from oil based raw materials which requires a great deal of energy to produce. The process of packing these meats requires machinery to ensure the efficiency and productivity of getting the meat to it’s final stages, the supermarket. Localized companies will use manual labour to pack their products but large, multinational companies produce such large quantities of beef they require quick, efficient methods of packing, mainly through energy hungry automation.
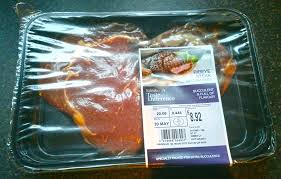
Dempsters Bread
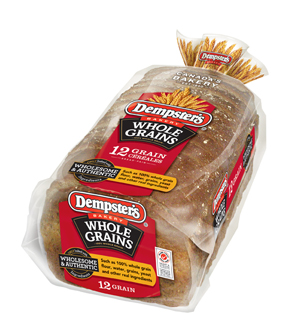
Dempsters is owned by a company called Maple Leaf foods which is located in Toronto, Ontario. It is a leading consumer food packaged company which operates across Canada and in the United States, United Kingdom, Asia and Mexico.
Production
Dempsters bread is produced locally and uses a mix of manual labour and automotive machinery to help produce the final product. To get a sense of the process, we can look at a ‘how it’s made video’ which will give a basic understanding and knowledge of how exactly bread becomes a finished product.
How it’s made Bread
As you can see there is a lot of manual labour that has been taken over by technology. The system of making bread requires a lot of mixing and baking, which uses a lot of heat energy in order to expand the yeast and make it more full. There are many different stages in the production of bread which require some form of energy and machinery to keep moving the materials to the next steps of production. Processing wheat requires planting, harvesting, transporting, cleaning, grinding and enriching the product which results in forms of fossil fuels being burned resulting in Co2 emissions to be released into the atmosphere.

As you can see, the production of bread is not as simple as many think but rather, it requires a complex system that enables all the ingredients of bread to form together creating the finished product which can then be packaged and transported off to retailers.
Transportation
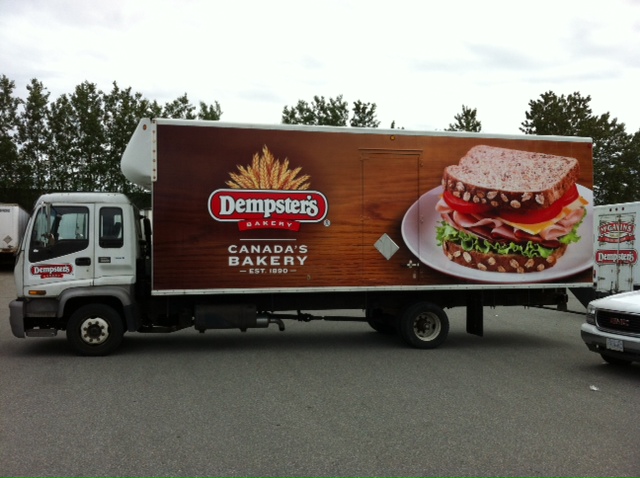
Since dumpsters bread is produced in regions throughout canada, transportation isn’t as severe as a lot of different staples that need to be exported and shipped from countries such as the U.S. The main source of transportation for Dempsters is through the use of trucks which don’t need to travel vast distances because the bread is being produced locally in most provinces across Canada. Of course there are greenhouse gas emissions and fossil fuels being emitted out of the trucks because they require a lot of fuel to run however, it could be much worse in the bigger scheme of things as other modes of transportation such as planes and shipping vessels require much larger quantities of energy. Most of the wheat comes from out of province, in places like Alberta and Saskatchewan as their climates allow for better wheat production. This wheat will then be shipped to local Dempster locations where the bread will be produced and shipped to retailers.
Packaging
Bread Packaging
Dempsters bread comes in a plastic bag which is sealed through the use of a plastic clip. plastic is an oil based product that requires the refining process to produce the materials for plastic production. These plastic bags are not made from recycled materials so the energy required starts at the refining process. The machinery required to produce the bags and then package the bread requires energy to operate and is a contributor to the consumption of fossil fuels and the release of Co2. All processes for the production of packaging require some form of technology and automation which requires energy, contributing to the consumption of fossil fuels and Co2 emissions.
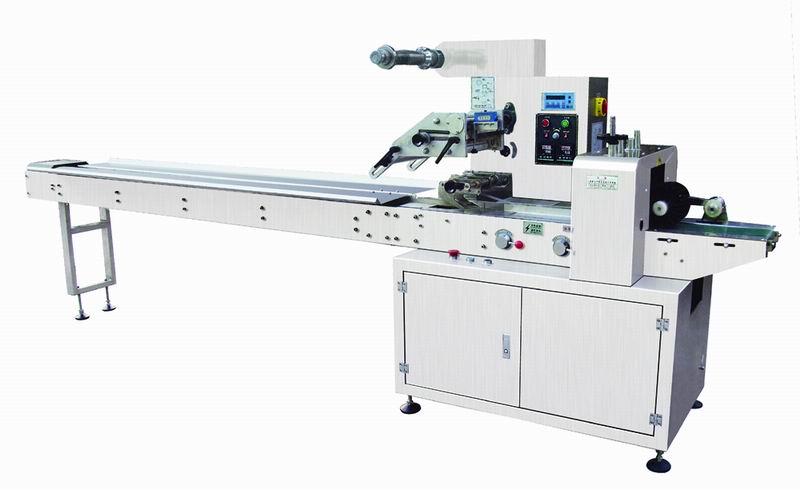