This week I took a first stab at modeling. I had my curves from the scanned Walter White segments, plus images of front, back, and side to work with.
My first attempt was to use the curves I had already drawn, plus any extras I thought would be necessary, and loft them into a surface. I spent a full day modeling a leg and arm this way, and although I eventually got the leg right, I never did manage to get the arm looking good. Below you can see the curves in black.
I
I eventually gave up on the curve-loft method. Now I am working with geometric solids, which I boolean to an approximate shape using other basic solids. Then I soften edges using fillet. Finally, I can tweak the object using box edit to get things just right. This process is working much better! Below, you can see a box for the body that I am starting to shape. It’s still very rough. The arm was started as a cylinder, and is ready to have a cuff added.
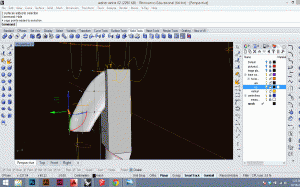
The image below shows the process for adding the cuff detail to the arm. I created a smaller cylinder, and scaled and placed it. Then I exploded the cylinder for the arm and the one for the cuff, and used blendsurface to connect them. The final step was to join and cap the 3 resulting surfaces, so I could fillet the edge at the bottom of the cuff. I’ll be doing roughly the same for the body next. Stay posted!
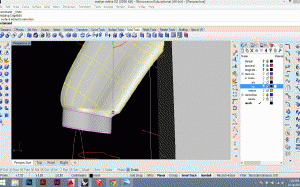