June(Zijun) Jiang | MEL Candidate | Dec 3, 2024.
Mentors: Tamanna Garg, CBRE
Abstract
The built environment sector is a significant contributor to global greenhouse gas (GHG) emissions, with embodied carbon comprising a notable share. This study evaluates opportunities to reduce embodied carbon in commercial building retrofits by analyzing roof and wall insulation materials. Key findings highlight trade-offs between material performance, cost, and environmental impact. Traditional materials, though cost-effective and widely available, often have higher lifecycle emissions, mitigated by some manufacturers adopting renewable energy production. Innovative materials offer superior thermal resistance but face challenges like high costs and technical complexities. Similarly, natural fiber-based materials have low carbon footprints but limited adoption due to research gaps and misalignment with building codes. The study emphasizes the need for regulatory frameworks, carbon intensity limits, and incentives to promote low-carbon materials. These findings aim to support Canada’s 2050 net-zero goals while advancing sustainable building practices.
Introduction
The built environment sector is responsible for more than a third of global energy-related carbon emissions. As global population and economic prosperity continue to rise, the demand for construction has escalated significantly.
Retrofitting offers a sustainable alternative to demolition, reducing embodied and operational carbon emissions. However, even energy-efficient retrofits contribute to embodied carbon emissions due to the materials and processes involved. For buildings already using electric heating, total life cycle emissions can increase by up to 170% compared to before the retrofitting. Additionally, at the current pace, retrofitting the entire commercial floor area in Canada would require 70 years, highlighting the critical need to expedite efforts and implement low-carbon solutions

Methods and Materials
- Materials Studied: See Table 1.
- Evaluation Parameters: R-value (ft²·°F·h/BTU), perm rating (perms); Material Cost (CAD) and Overall carbon footprint (kg CO₂ eq ) with standardized baselines of R-30 for walls and R-50 for roofs across an area of 2,000 sf.
- Lifecycle assessment (LCA) data were extracted from Environmental Product Declarations (EPDs) to evaluate the embodied carbon of each material.
- Case studies and literature reviews were utilized to assess innovative materials, as well as to analyze current incentives and regulatory frameworks supporting low-carbon solutions.
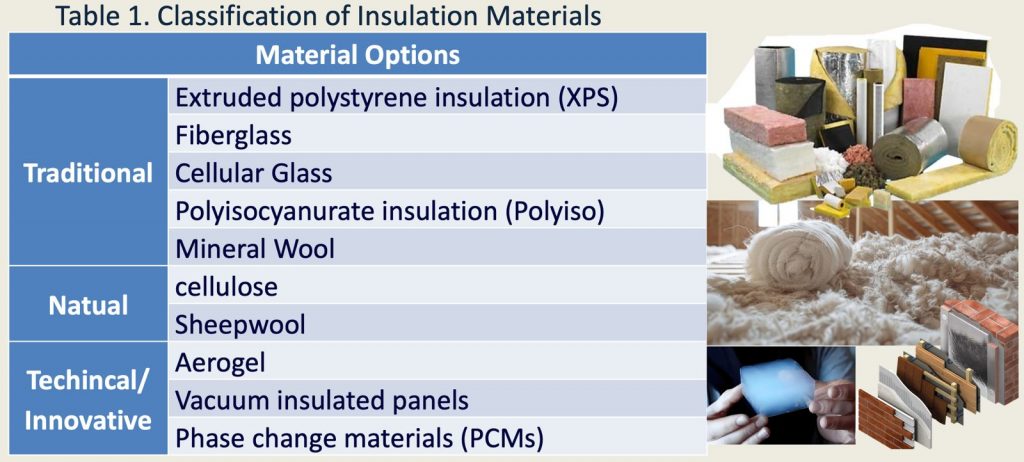
Results & Discussion
Traditional Materials: Widely used options like XPS and mineral wool are cost-effective and readily available but have higher lifecycle greenhouse gas (GHG) emissions. Some manufacturers have reduced their carbon footprint by transitioning to 100% renewable energy in production, showcasing the potential of clean manufacturing practices.
Natural Materials: Materials such as sheep wool demonstrate low carbon footprints and high sustainability potential. However, adoption remains limited due to scalability issues and misalignment with current building codes. Expanded research and alignment with regulatory frameworks could help unlock their potential.
Innovative Materials: Advanced solutions offer superior thermal resistance and reduced material use. Despite these benefits, high production costs, technical complexity, and limited availability pose significant barriers to widespread adoption.
Policy, Incentives, and Regulatory Gaps: A lack of comprehensive incentives and regulations targeting embodied carbon hinders the adoption of low-carbon materials. Current policies in Canada primarily focus on operational energy use, with limited consideration of lifecycle emissions.

Conclusions and Recommendation
- Materials:
- Polyiso offers the best overall balance, due to its low embodied carbon emissions and cost efficiency.
- XPS is another good for projects requiring durability and performance at a reasonable cost at low temperatures.
- Regulations:
- Prohibit high-GHG materials and set carbon intensity limits for key construction materials.
- Fast-track permitting for low-carbon retrofits and require pre-demolition audits to promote material reuse.
- Establish an EPD database for better material selection.
- Incentives:
- Offer tax rebates for manufacturers developing low-carbon materials and grants for retrofits with exceptional carbon performance.
- Provide financial incentives for using low-embodied-carbon materials in certified green buildings.
- Implement training programs on lifecycle assessments (LCAs) and educate stakeholders on embodied carbon.