Plastic waste management has become a serious issue over the last few decades. In 2019, the total amount of plastic produced since 1950 totaled just over 9.5 billion tons, and plastic production hasn’t slowed down, as 400 million tons were added to that in 2020.
The chemical bonds that make up plastics are hard to break and do not degrade in the environment quickly. This makes plastic waste challenging to deal with, leading to a large amount of plastic being discarded or incinerated.
While people have been recycling since the late 1980s, only about 6% of annual waste is recycled, and only a further 20% of that stays recycled. Current recycling methods consist of mechanical recycling, a process by which the plastic is ground or melted down into a new product, or chemical recycling, a process by which chemical additives break down the plastic into more manageable pieces to be used as raw material. However, both methods are not environmentally friendly or cheap, leading to a high volume of plastics that are not recycled (see below).
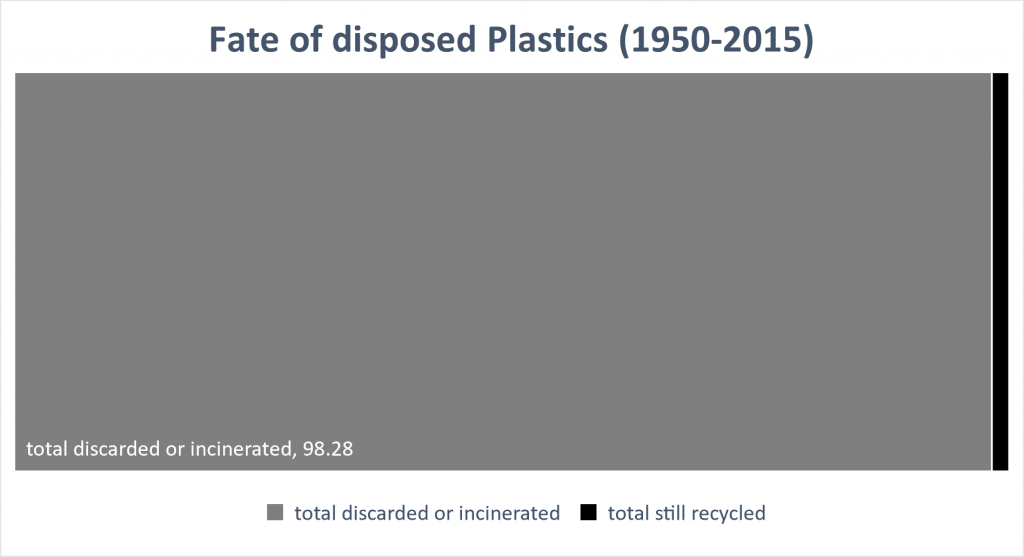
The final fate of plastics over 65 years. only 1.72% of plastics remain recycled.
Finding new ways to deal with plastic waste is a heavy focus for environmental scientists, leading to catalysis, electrochemistry, and photochemistry developments. One such method, developed by Dr. Resier and his team at the University of Cambridge, has found a way to deal with this waste in an environmentally clean way. Using a perovskite (PVK) based photocathode and a copper-palladium alloy anode in combination with a CO2 reduction catalyst, they transformed PET plastics and CO2 into a variety of useable fuels and by-products, such as carbon monoxide, hydrogen gas, and glycolic acid.
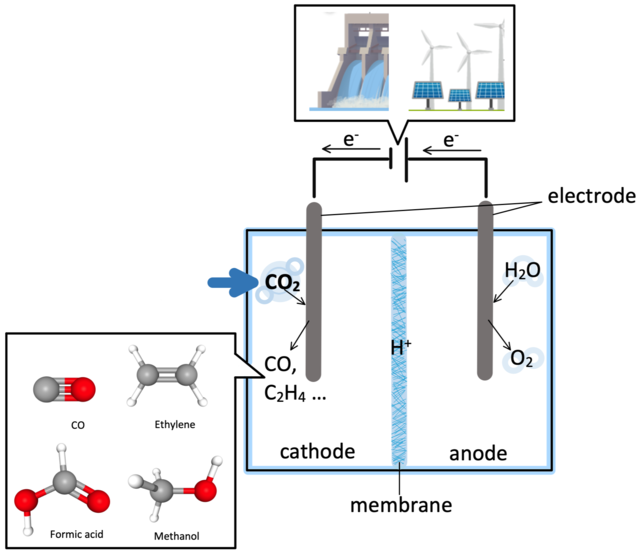
Electrochemical pathway of CO2 reduction into CO and byproducts.
The photoelectrochemical system works upon sunlight exposure under zero applied voltage and generates products 10-100 times faster than other catalytic methods. Further, the catalyst system is not sensitive to the introduction of bio-organic molecules; in fact, the presence of small amounts of food products could increase the activity of the system.
However, this process is anything but cheap. The copper-palladium alloy anode is not cheap to fabricate, and the materials required are rare, palladium being over 15 times rarer than platinum. This increases startup costs, which is not favorable to most companies who could instead dump the waste.
While advancements in this technology are still needed, there is a positive outlook for the future of plastics and environmental contaminants. We may yet be able to save our fragile, yet vital planet from our own advancement.
Tristan Ruigrok