It should not be a surprise to people that it can take over 500 years for UV radiation – light from the sun to break down a piece of plastic. But what if there is a faster way to break down single-use plastics?
Researchers at the University of California, Berkeley invented a new way to decompose consumer plastics in a short amount of time, simply with heat, water, and nano-dispersed enzymes.
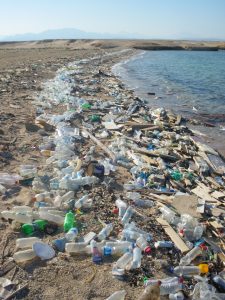
Plastic waste covering the shoreline. Source
UC Berkeley professor Dr. Ting Xu and her research group developed a nanoscale enzyme that can eat away at the polymers in plastics. These nanoscale polymer-eating enzymes can be embedded into plastics during manufacturing. The enzymes were wrapped around plastic resin beads. These beads are melted and can be manufactured into single use consumer plastics. To prevent the enzymes from activating when not required, a random heteropolymer (RHP) coating is applied to hold enzymes without restricting the flexibility of tensicity of the plastics.
Xu likened this process to organic composting. By adding water and heat, the RHP polymers is removed and starts eating away the polymers into smaller subunits.
The research conducted by Xu and her group found that the enzymes took about a week to degrade most of the plastics. Polylactic acid (PLA) and polycaprolactone (PCL) based plastics embedded with nanoscale polymer eating enzymes are able to break down the polymer chains into smaller molecules, such as lactic acid.
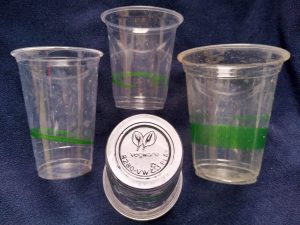
Plastic cups made from biodegradable plastics. Source
It is clear there is still more research needed in this field. Currently, Xu is developing other modified RHP-wrapped enzymes that can stop the degradation process at specific points in it’s degradation so that the polymers can be recycled into new plastics.
“[Humans] are taking things from the Earth at a faster rate than we return them,” said Xu. “Don’t go back to Earth to mine for these materials, but mine whatever you have, and then convert it to something else.”
As consumers, we can play an important role reducing our consumption on single use plastics and create a more sustainable environment for ourselves and future generations.
Raymond Tang