plastics
Plastic is one of the most pervasive materials on the planet. It is used in industrial production, everyday products, and all types containers. It is omnipresent in a variety of industries including construction. Plastic is malleable, durable, formable, pliable, water resistant, lightweight, and strong. It is arguably the most sophisticated and heavily engineered material we use on a daily basis. These traits, and the material’s ubiquity are the very things that make plastic a problem. Humans are generating more plastic trash than ever and using it at an alarming rate. The material is inexpensive and we consider it cheap and disposable. Very little plastic gets recycled.
HiLo Lab is interested in turning plastic into a viable material for construction. This research began as an exploration in vacuum forming (building off research on variable vacuum forming begun by HouMinn Practice). Our team eliminated the need for formwork when it turned to inflation as a method of transformation. This approach offers advantages. Flat panels are transformed using heat and pressurized air. This eliminates the need for formwork and renders the fabrication process virtually waste free. The material used is light weight yet strong. Finally, the process provides a use for plastic waste and could provide incentive to collect discarded plastic, or motivation to recycle.
spanning plastic
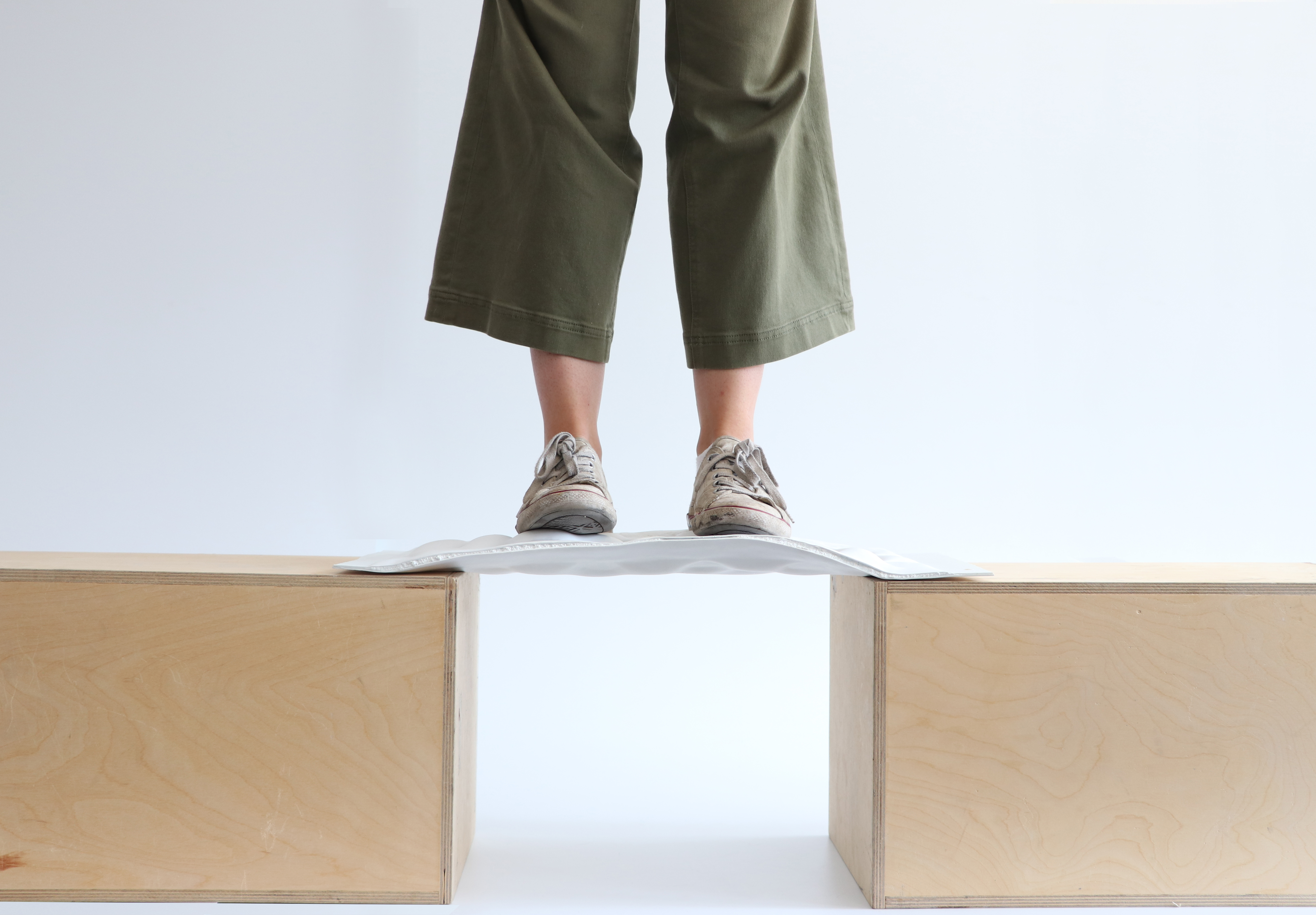
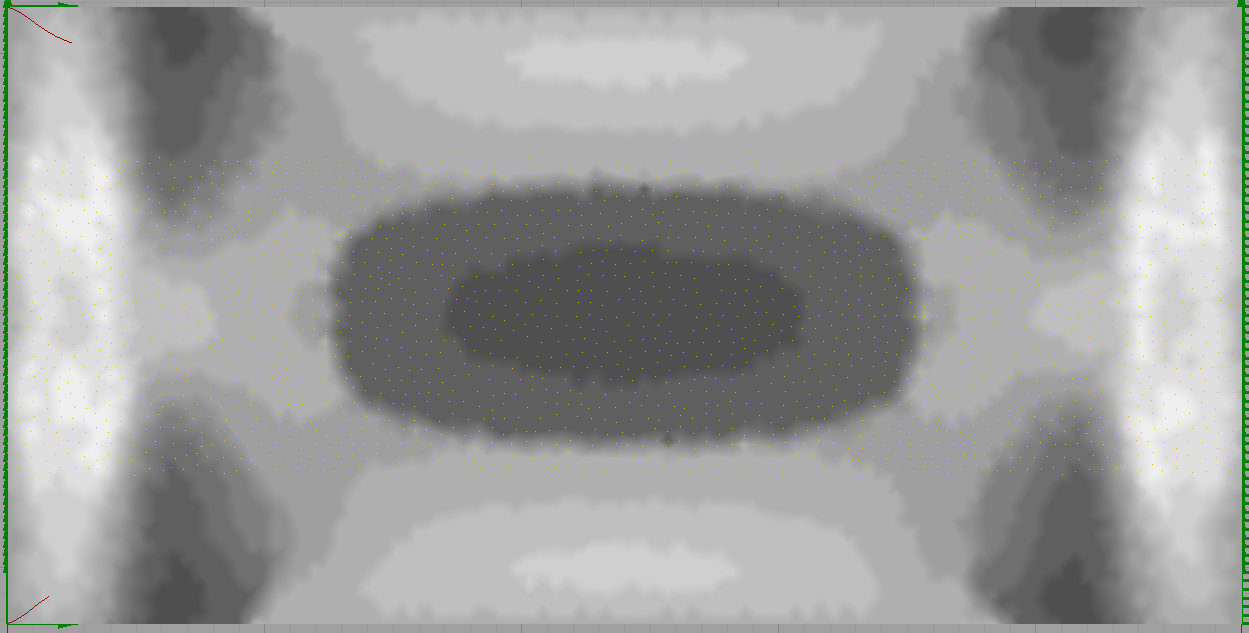
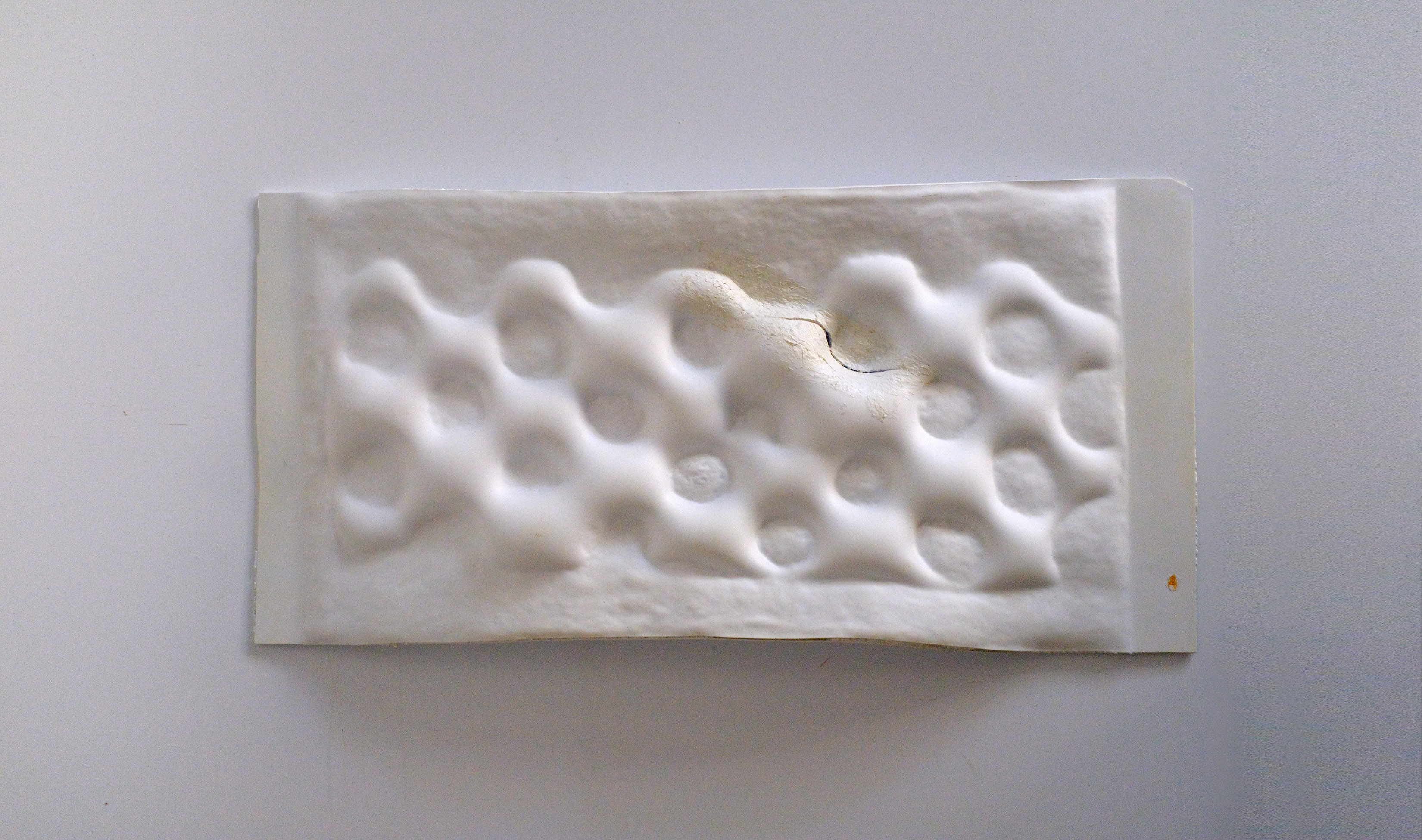
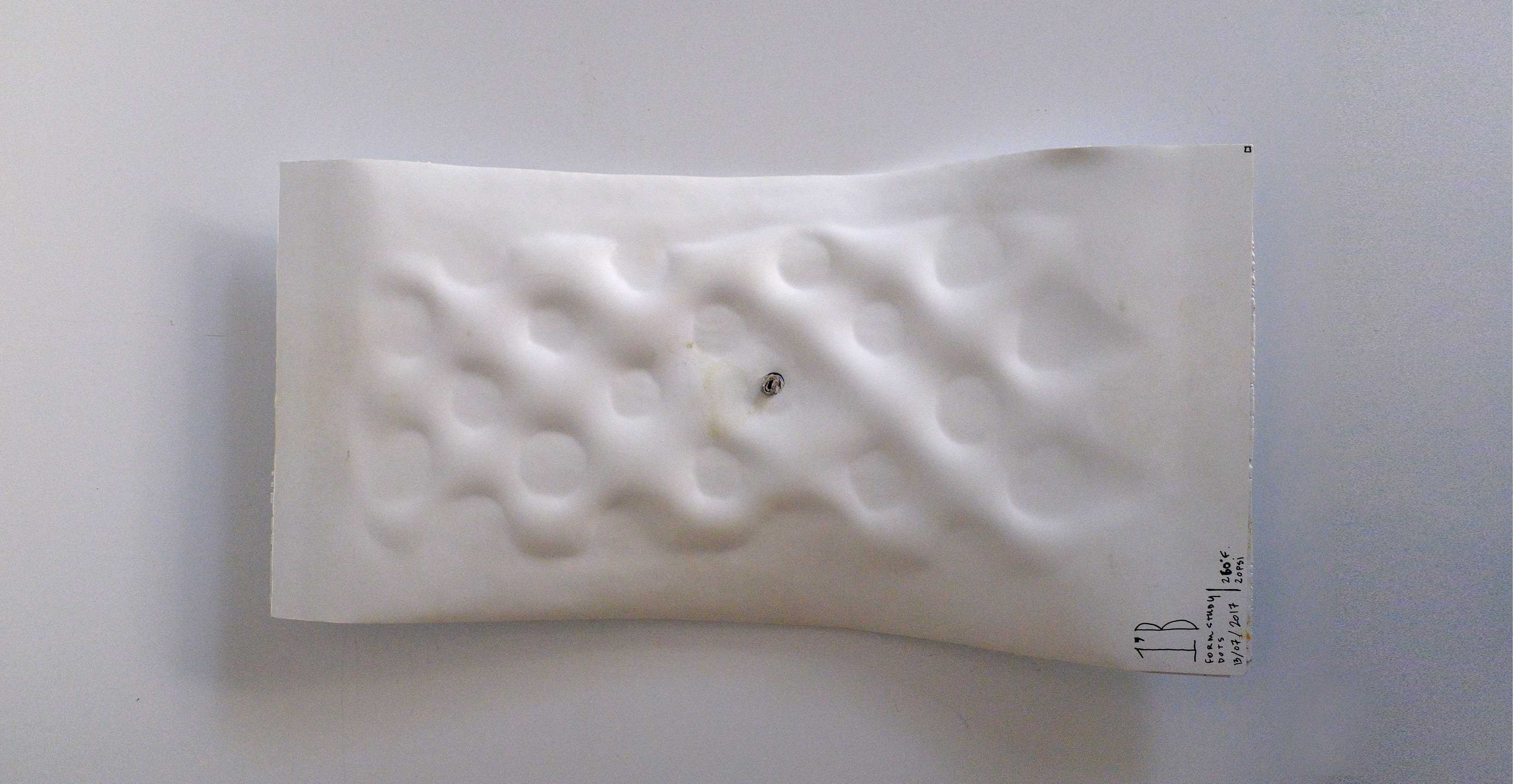
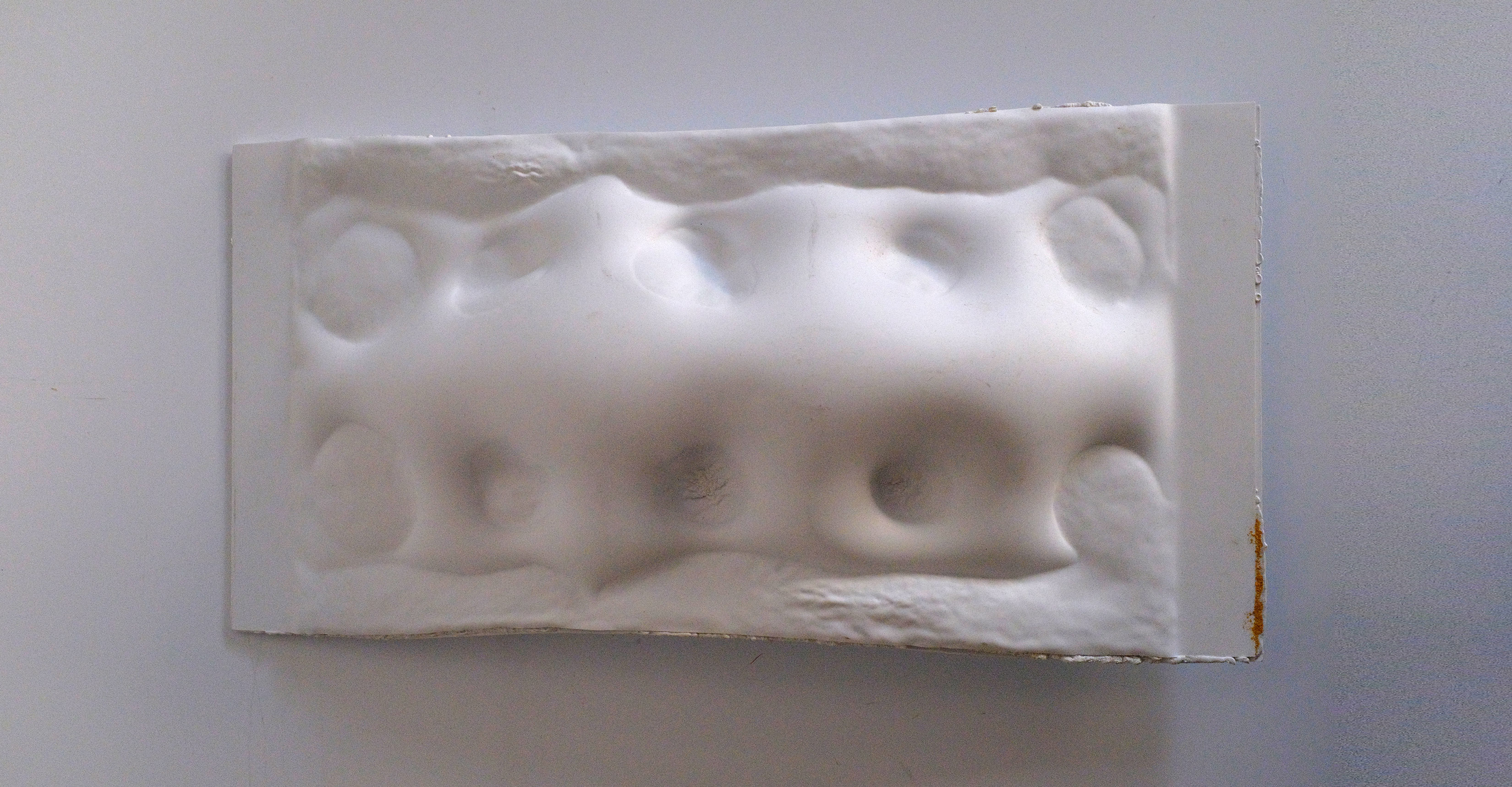
contributors
Stuart Lodge, Sebastien Roy, Graham Entwistle, Blair Satterfield