A scratch on your car may no longer need a trip to the auto-shop. Simply applying heat or light could remedy this issue. This idea could soon be a reality using vitrimers, a new class of plastics that have thermal and chemical stability, but can also be self-healing on a small scale and fully recyclable on a larger scale.
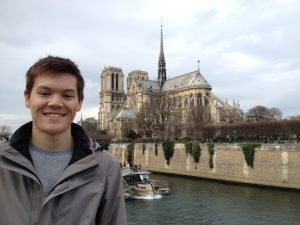
Taylor Wright from Dr. Wolf’s group at UBC. Source
In 2018, at the University of British Columbia, Taylor Wright under the supervision of Dr. Michael Wolf investigated the photoactive self-healing properties of vitrimeric copolymers.
Photoactive materials undergo physical and chemical changes in response to illumination. The development of responsive materials to both heat and light were explored for the first time through the incorporation of functional molecular groups into the polymeric backbone of these systems.
Wright and Wolf’s focus on the molecule’s response to light also offered a new aspect into vitrimeric research compared to the previous studies, that exclusively focused on the vitrimers’ response to heat.
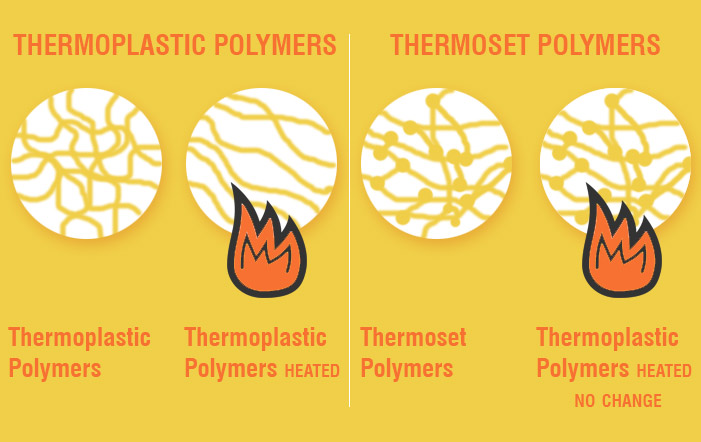
Figure 1. Comparison of thermoplastics and thermosets upon heating. Source
So what exactly are vitrimers? Vitrimers are a new class of polymeric material that was first created in 2011 by a Polish physicist, Dr. Ludwik Leibler. By combining characteristics of thermosets and thermoplastics, Leibler was able to develop a material that is strong and durable, yet moldable and recyclable.
Thermoplastics are made of plastics linked by intermolecular forces. They can be easily molded and shaped under heat, then cooled down to produce the final structure. This allows for ease when it comes to processing. Additionally, this property allows them to be recycled to produce new products.
Conversely, thermosets involve irreversible cross-linking, connecting the backbones of the polymer chains with molecular bridges. This results in enhanced chemical and heat resistance, making the material less susceptible to stress-cracking. However, due to their cross-linked bonds, these materials do not melt upon exposure to heat, unable to remold and recycle.
Vitrimers combine the best properties of both materials; structural integrity is improved through cross-linking, as well as self-healing and fully recyclable properties.
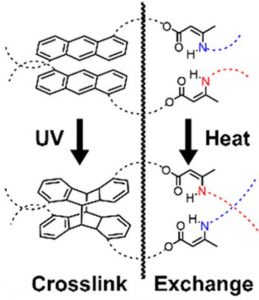
Figure 2. The molecular structure of the photoactivated vitrimeric copolymer created by Wright and Wolf. Source
As seen above in Figure 2, the vertical wiggly line splits the system into the two unique parts that make this a copolymer. The left side shows the aromatic anthracene molecule that crosslinks into a dimer in response to UV radiation. The amine on the right side behaves like a more traditional vitrimer and responds to heat to form reversible exchanges.
Originally, their aim was to create a single polymeric system that responds to both heat and light simultaneously. However, during their research, they found that amines directly bonded to the anthracene molecules simply do not engage in the bond exchange process. They believed the electronics of the ring alters the behaviour of the molecule in comparison with non-aromatic amines.
Studying the photodimerization and thermally exchangeable functionalities of the copolymer based on the vinylogous urethane vitrimer, the self-healable properties can be seen in the video above. Self- healing polymers are a class of materials that enable the repair of micro-scale damage in the coating, ultimately restoring the passive state of the metal substance. This enables reprocessability or longer lifetimes in cross-linked polymeric materials. The systems containing anthracene undergo self-healing through reversible reactions, allowing monomers and polymer chains to link and unlink.
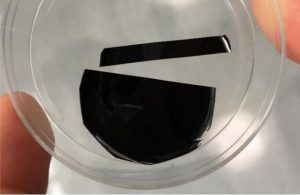
Figure 3. Polymer sample, P2, mounted on a glass slide. A scratch from a razor blade can be observed. Source
Wright and Wolf tested the modification of surface properties by using a razor blade to scratch a polymer sample (that Wright denoted as P2), that was mounted on a glass slide. By using optical microscopy, the scratches were observed as dark lines crossing the sample, as seen below in Figure 4. The scratches were seen to decrease in width and ultimately close during heating through a series of expansions and contractions of the material, which can be seen in the video above.
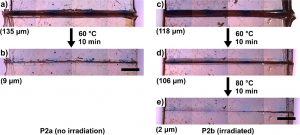
Figure 4. Optical microscope image of (a) sample P2a initial scratch, (b) P2a after heating (c) sample P2b initial scratch, (d) and (e) P2b after heating. Black scale bar is 300 μm. Source
These specific Wright and Wolf vitrimeric copolymers will not be scaled up for commercial use, due to the difficulties of incorporating the two components of the copolymer together. However, the general idea of vitrimeric materials has “almost limitless applications”. For example, they can be incorporated into products that have a long lifetime, such as shipping materials and plastic stadium seats which can be recycled into new products once they start to deteriorate.
Additionally, Wright is currently working on vitrimers that start as a viscous liquid, much like thermoplastics, that can be easily molded and processed. This possible advancement will provide more flexibility with processing the starting material and ease in the synthesis process.
~Brina, Isla and Taiki (Group 4)