A 3D printer creating a new part. Photo by Osman Talha Dikyar on Unsplash.
One of my favourite parts of the MECH program is the design project courses we have every year. It feels like these are what all of the theoretical studying in lectures are meant for. They encourage critical thinking, creativity, and problem solving skills, and are very transferrable to what work might look like after graduating. This post is about each of the project courses and my experiences through each one.
MECH 220 – Technical Skills Practicum
This course is the first thing you’ll take as a new MECH student! It’s structured as four one-week modules that cover machining, engineering drawings, computer aided design, and electronics. As a result, you will create a magnetic levitation (MagLev) that showcases your learning over the entire month. To this day, this is still one of my favourite courses in MECH. The machining module was my favourite, where we got to use the mill, lathe, press, and various hand tools. It felt like we were real engineers, not just students studying equations. I was also able to bond with my classmates during this time, as we would see each other every day, all day, working together.
MECH 223 – Mechanical Design
MECH 328 – Mechanical Engineering Design Project
For the third year project course, we were given an open ended problem and had freedom to choose what design to theoretically create. The prompt was to remove combustion engines from a product, and replace the energy source with something more sustainable. My group chose to electrify search and rescue (SAR) boats. Since this project has more of a focus on stakeholder consultation, we were able to meet with and tour a SAR boat thanks to Royal Canadian Marine SAR volunteers. It was interesting to explore something I didn’t know much about, but I wish that there was a build component to the project.
MECH 45X – Capstone
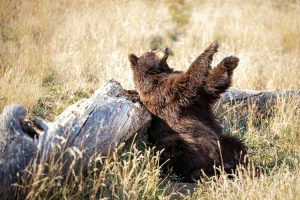
A current solution – which we’d like to make higher tech! Photo by Stephanie LeBlanc on Unsplash
It’s currently my final year, and I’m just starting to ramp up my Capstone project. In this course, you are able to choose or rank what prompt you are interested in, and have more freedom with choosing your team members. The projects all interface with real clients, and typically you would build a working prototype by the end of the year. For my capstone, my team is working on designing a better wildlife hair snag to collect DNA samples for biological research! It’s still early on in the process, but I’m looking forward to building something that will be used in the real world.
If you like solving design problems and thinking of novel solutions, you will enjoy the project courses in MECH! From participating in these projects I feel better equipped and more confident about my knowledge and experiences going into the industry. I would encourage anyone to make the most of this time, where we can explore our interests and have design control over our work, which is not always the case post-grad.